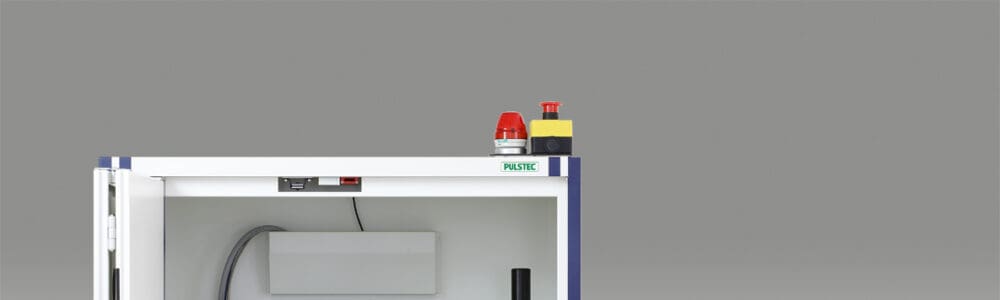
For many years, only one technique has been used for X-ray residual stress analysis: the sin2𝜓(sin squared Psi) method. This method was developed in the 1920s, and is still widely used today. In fact, many manufacturers sell measurement devices that use the sin2𝜓 method. Committed to innovation, Pulstec takes a different approach to residual stress analysis: the cosα (Cosine Alpha) method.
Table of Contents
What Is the cosα Method?
The cosα method is a way to measure residual stress via X-ray diffraction. The unique cosα technology was developed at Kyoto University in Japan in the 1970s. Although this technology was revolutionary, it did require a highly sensitive 2D sensor, and during that time, 2D sensor technology was not a commercially viable option.
Pulstec was the first company in the world to successfully commercialize this device. In the 2010s, we developed our own X-ray residual stress analysis device using the cosα method. Our equipment provides a single-incident X-ray angle and a high-sensitivity 2D sensor (the high-sensitivity sensor technology that’s found in Blu-ray™ disc testers.)
So, what’s the difference between the cosα method and the well-known sin2𝜓 method?
cosα Versus sin2𝜓
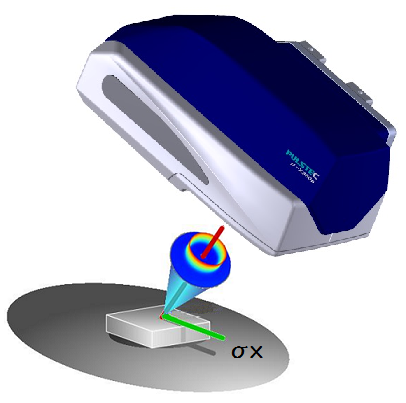
The main distinction between the sin2𝜓 method and the cosα method is simply the difference in the dimension of the sensor.
The sin2𝜓 method uses a zero- or one-dimensional sensor to acquire a portion of the diffraction Debye-Scherrer ring (0 or both 0/180 degree portion of the ring), and then changes the angle of incidence of X-rays to acquire crystal distortion.
The cosα method uses a two-dimensional sensor to acquire the entire Debye-Scherrer ring (the entire circle) at once, and then obtains the crystal distortion. There is no need to change the angle of incidence. As a result, the cosα method equipment has many advantages.
Advantages of the cosα Method
- Small Footprint: With the cosα method, there is no need for a goniometer.
- Fast Measurement: The cosα method can measure residual stress in 60 seconds(If Ferrite). Additionally, there is no need to tilt the X-ray beam and re-acquire the diffraction.
- Low X-Ray Output & Air Cooling: There is no need for an external water chiller.
- Better On-Site Measurement Capabilities: cosα equipment makes it much easier and faster to measure large samples on-site.
- Easy to Transport: The equipment is lightweight, which makes it easy to move it between locations.
- Hassle-Free Sample Alignment & Operation: There is no need to fine-tune the imaginary center, because the X-ray is not tilted. Additionally, only one training session is needed to learn the equipment.
- Stress-Free Integration (Inline or Robotics): Our specialists at Pulstec will even walk you through the integration process.
Who Can Use cosα Equipment?
cosα equipment is widely used in many industries, especially by Japanese automobile manufacturers and suppliers.
How This Equipment Has Made an Impact in the Automotive Industry
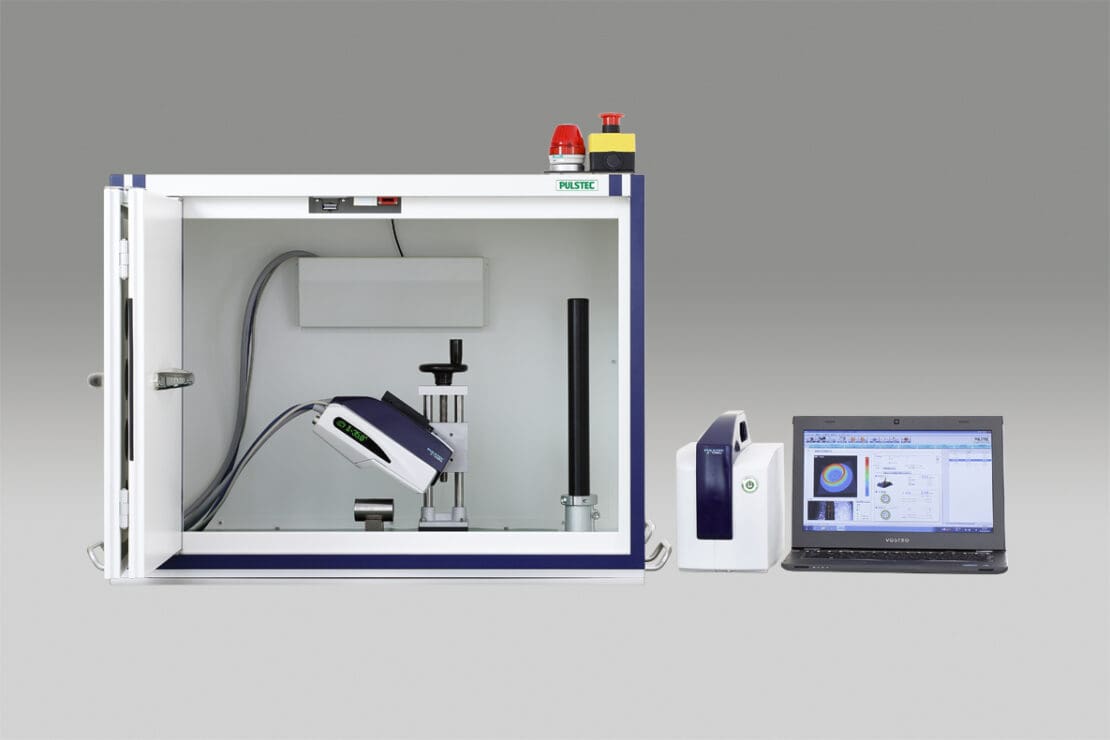
In the past, those working in automotive research and development (R&D), quality assurance, and manufacturing needed to measure residual stress.
However, only the R&D department could handle the sin2𝜓 method equipment because the operation was too complex.
The R&D department had to not only measure residual stress in parts sent from factories all over the world, but also proceed with their own projects in parallel.
Because of this, it was not uncommon to have to wait several weeks to measure these parts. And, if the results were not satisfactory, the produced parts were rejected, resulting in a huge quality loss.
With Pulstec’s cosα equipment, the process has become much faster. Plus, our equipment is easy to handle/operate. All it takes is just one simple training session.
Pulstec’s Impact
An R&D department based in Japan tried our innovative technology, and immediately gave us feedback. We’re happy to say that they have significantly reduced quality-related losses in their department. We believe that our cosα equipment will not only contribute to the R&D department, but also to the reduction of quality loss in the QA and manufacturing departments.
Contact Pulstec Today
Do you have questions about our X-ray residual stress analyzer? Contact us today to schedule a consultation or demo.