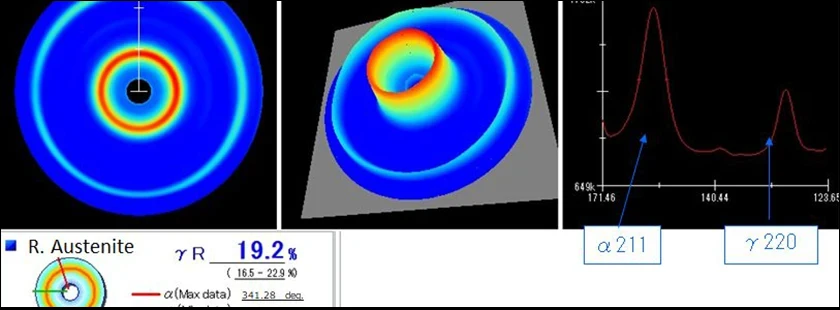
Retained austenite can significantly influence the hardness, strength, and wear resistance of steel, so accurate measurement helps to ensure steel components meet the desired specifications and perform reliably in their intended applications.
In this blog, we’ll compare some of the different ways of measuring retained austenite and discuss why X-ray diffraction is the most balanced method.
Methods of Retained Austenite Measurement
Microscopy
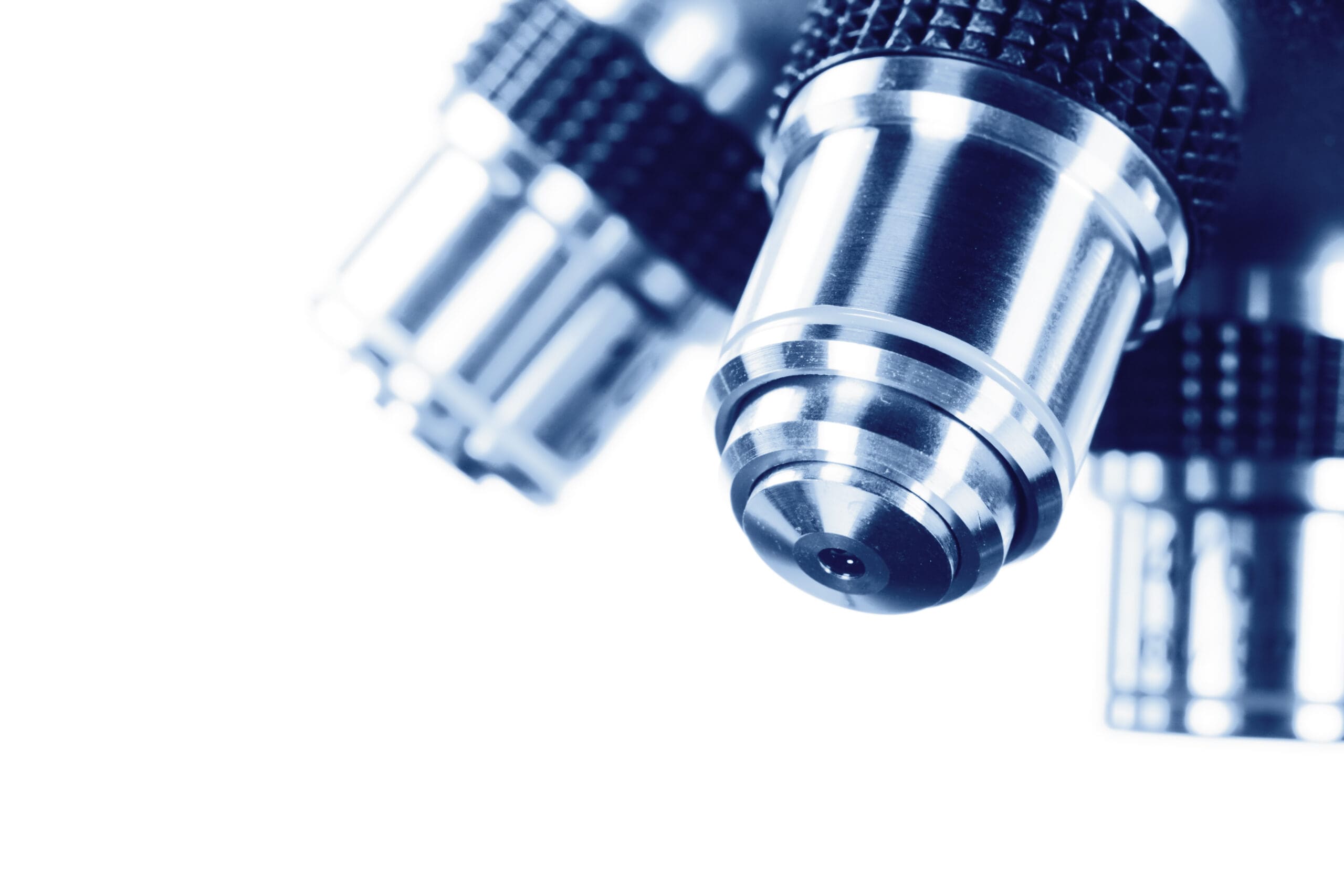
Techniques like optical microscopy and scanning electron microscopy (SEM) are sometimes used to identify and quantify retained austenite. The steel sample is typically etched to reveal the microstructure, and retained austenite appears as distinct phases that can be differentiated from other constituents like martensite and ferrite.
This method, particularly SEM, can provide high-resolution images that allow for detailed analysis of fine microstructural features. It can be used on many different materials and under many different conditions.
The downside is that both microscopy methods require meticulous sample preparation, including polishing and etching, which is time-consuming and can potentially damage the sample. These methods also primarily provide qualitative data—quantitative analysis can be challenging and less accurate than other methods.
Magnetic Induction
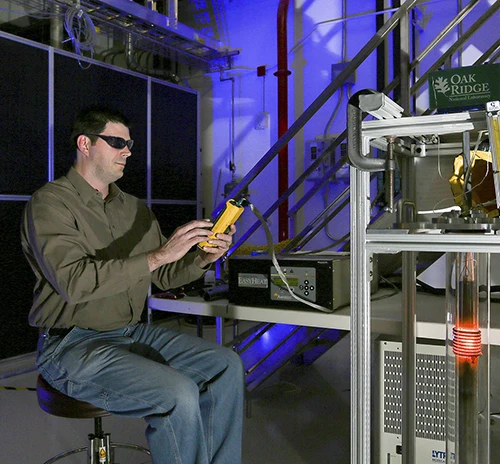
Austenite is non-magnetic, whereas phases like ferrite and martensite are magnetic. By applying a magnetic field to the steel sample and measuring the response, you can quantify the amount of retained austenite based on the difference in magnetic properties.
This method can be done rapidly, making it suitable for inline or high-throughput testing. It doesn’t alter or damage the sample and requires minimal sample preparation. However, the method can be less accurate than X-ray diffraction, especially for low levels of retained austenite. Accuracy can also vary depending on the composition and heat treatment of the steel, requiring calibration for different materials. Surface coatings or contamination can also impact accuracy.
Image Attribution: "Using induction heating to observe the behavior of metals in high magnetic fields" by oakridgelabnews is licensed under CC BY 2.0.
Neutron Diffraction
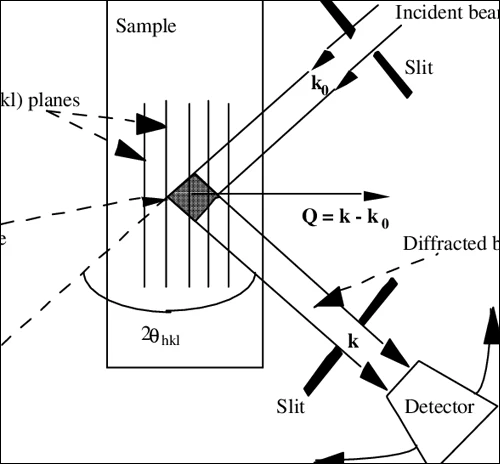
In neutron diffraction, neutrons penetrate deeply into a steel material, interacting with the atomic nuclei and producing diffraction patterns. These patterns are analyzed to quantify the retained austenite and distinguish it from martensite and ferrite phases.
Neutrons can penetrate much deeper than X-rays, providing information about the bulk properties of the material without altering the sample. The downside is that it requires access to a neutron source, which is typically available only at specialized research facilities and is expensive to obtain. The process can also be lengthy, limiting its practicality for high-throughput testing.
Image Attribution: "Set-up-of-a-neutron-diffraction-experiment" by Gianni Albertini is licensed under CC BY-SA 4.0.
Thermal Analysis
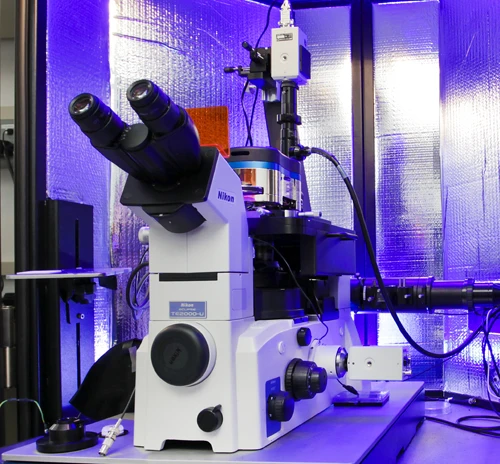
Another way to measure retained austenite is through thermal analysis methods like Differential Scanning Calorimetry (DSC) and dilatometers. These methods measure retained austenite by monitoring changes in the material’s thermal properties. DSC measures heat flow associated with phase transitions, while dilatometers measure dimensional changes as the material is heated or cooled.
Like some other methods discussed in this article, DSC and dilatometers are non-destructive and precise. However, they require careful sample preparation to ensure accuracy, require expensive thermal analysis equipment, and can be lengthy.
Image Attribution: "Ztherm Modulated Thermal Analysis" by oakridgelabnews is licensed under CC BY 2.0.
Mossbauer Spectroscopy
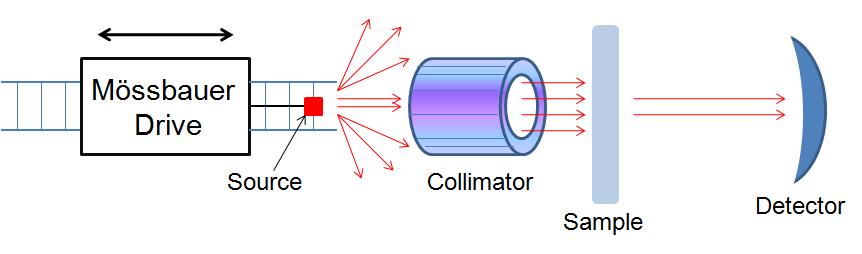
Mossbauer spectroscopy uses the resonant absorption of gamma rays to analyze a material’s atomic and magnetic structure. In the context of retained austenite measurement, different iron phases can be distinguished based on their unique gamma-ray absorption patterns.
Although this method offers detailed insights into the magnetic and electronic environments of iron atoms in a non-destructive manner, it requires specialized equipment that can be expensive and hard to access. It’s only useful for iron-containing samples, and it’s also a lengthy process, so it’s not ideal for rapid testing applications.
Image Attribution: "Mossbauer Spectrometer" is licensed under CC BY 2.0.
Electron Backscatter Diffraction
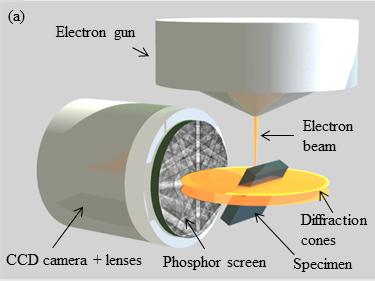
Electron Backscatter Diffraction (EBSD) provides crystallographic information from a sample’s surface. This method can identify and quantify different phrases, like austenite, ferrite, and martensite, by analyzing the diffraction patterns of backscattered electrons.
EBSD offers detailed microstructural analysis with high spatial resolution and can accurately distinguish between austenite and other phases. However, it requires meticulous surface preparation to obtain clear diffraction patterns, and it primarily analyzes the surface layer, with limited depth penetration compared to other techniques.
Image Attribution: "EBSD Setup Graphic" by Stefano Vespucci et al. is licensed under CC BY 4.0.
X-ray Diffraction
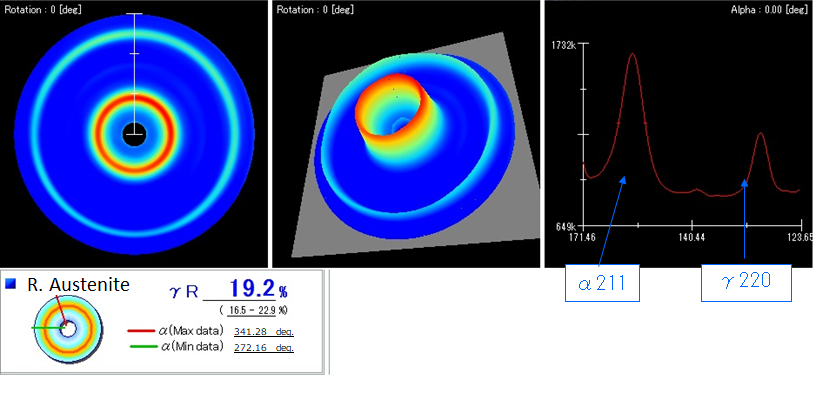
X-ray diffraction is one of the most reliable ways to measure retained austenite, especially amounts of 20% or less. In this method, retained austenite is measured by analyzing the diffraction patterns of X-rays scattered by the crystal structures in steel. Different phases produce distinct diffraction peaks, allowing for their identification and quantification.
This method is non-destructive, fast, highly accurate, and applicable to various sample shapes and sizes. You can hit the X-ray directly to the bare surface and get results in just a few minutes. The only downside is that it primarily analyzes surface layers and has limited penetration depth. However, some workarounds exist, including gradually removing surface layers and performing sequential measurements or using thin samples.
Learn More About Pulstec’s μ-X360s XRD Analyzer
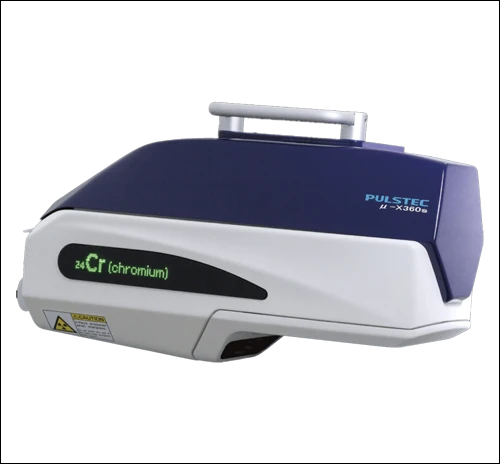
Pulstec is an industry-leading manufacturer specializing in X-ray equipment. Our μ-X360s X-ray analyzer allows you to measure retained austenite in steel samples in as little as 90 seconds and residual stress in just 60 seconds. The equipment is easy to use, lightweight and portable for field measurements, and uses low X-ray power while still remaining accurate.
Please contact us today to learn more about our analyzer or to request a free demo. You can also visit our blog for more retained austenite and X-ray diffraction resources.