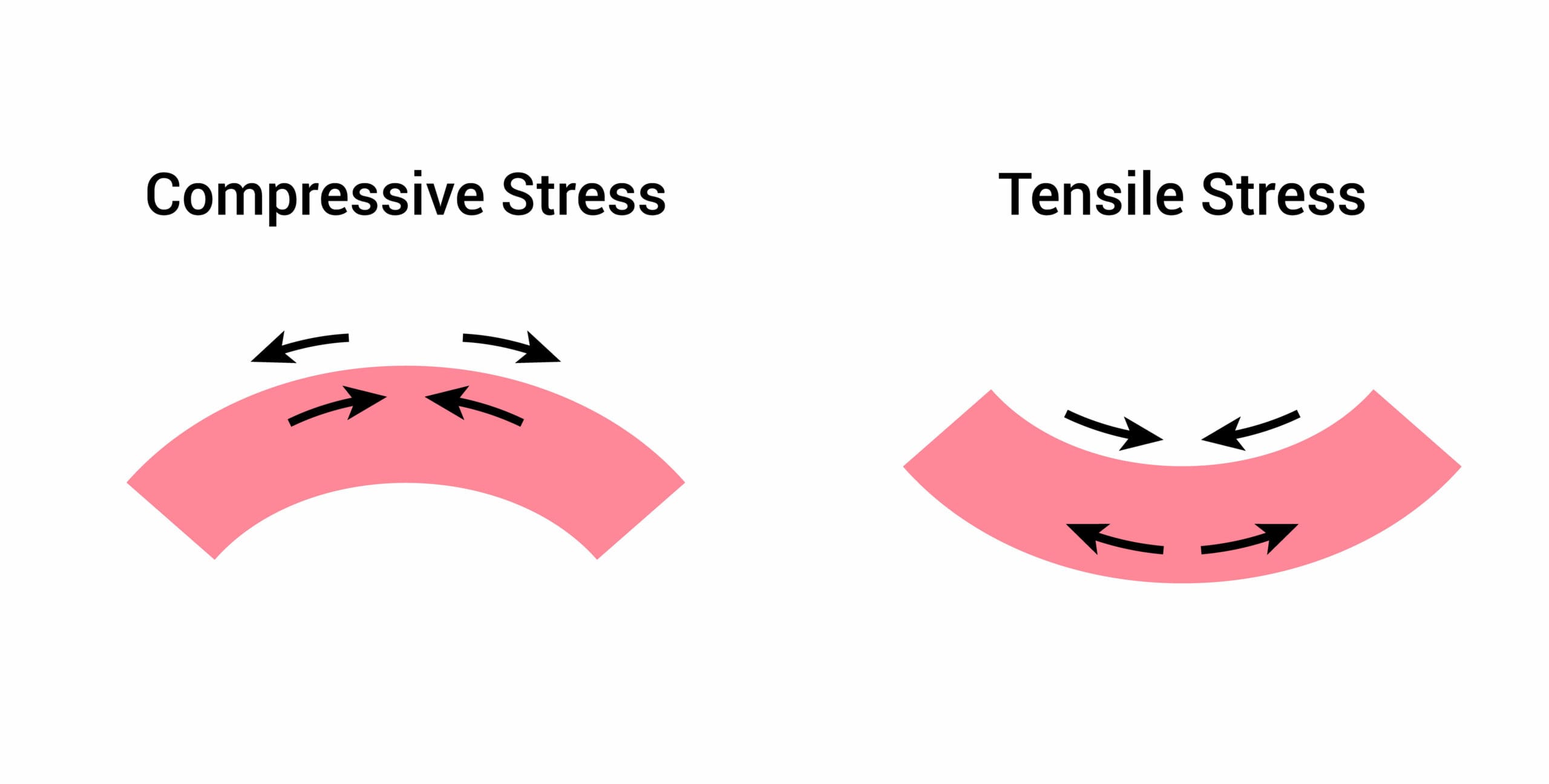
Every metal working process, including grinding, thermal treatment, bending, and peening, leaves its mark in the form of residual stress.
These unseen forces can either be your ally or your downfall, as they can affect the longevity and reliability of your products and components—this is why it’s so crucial to measure and understand them on a deeper level.
In this guide, we will provide an overview of the two primary types of residual stress: compressive and tensile.
Compressive Residual Stress
What Is Compressive Residual Stress?
Compressive residual stress exists within a material, even without any external force acting upon it— this is why the stress is “residual.” It’s a “squeeze” or “inward push” within the material, if you will, and unlike its sibling (tensile residual stress), it isn’t always bad news.
In fact, in many applications, compressive stress is viewed as beneficial.
While too much of any stress within a material can be a problem, compressive stress can actually improve the fatigue life of a material, making it more durable and acting as a buffer against tensile stresses that might lead to cracking or other forms of damage.
Compressive residual stresses can be intentionally induced through various manufacturing processes. Shot peening and laser peening, for instance, are two common processes that can intentionally induce a compressive residual stress.
Causes
As mentioned earlier, compressive residual stresses can play a beneficial role in reinforcing the longevity and durability of components, particularly in metallurgy and manufacturing.
Here are several causes of compressive residual stresses in materials and components:
- Shot Peening: This cold-working process bombards the component’s surface with small spherical shots. The dents caused by the shot create a layer of compressive stress, enhancing fatigue strength.
- Laser Peening: Similar to shot peening, this process uses powerful laser pulses to generate a shock wave on the component’s surface, resulting in a compressive stress layer much deeper than shot peening can achieve.
- Heat Treatment: Certain heat treatments, like tempering and quenching, can induce compressive stresses—rapid cooling contracts the surface faster than the core, producing a compressive stress layer.
- Surface Rolling: This process involves pressurizing a ball or roller onto the component’s surface, displacing and cold working the surface material to create compressive stress.
- Stress Relief Annealing: In this process, a material is heated below its transformation temperature, then slowly cooled to reduce tensile stresses and induce compressive stress.
The primary takeaway here is that compressive residual stresses are essential for enhancing component durability and are commonly used in automotive, aerospace, and additive manufacturing for additional strength. In PBF (Powder Bed Fusion) additive manufacturing, parts after printing are always in tensile stress, so it is essential to heat treat them to convert to compressive stress.
What Is Tensile Residual Stress?
Tensile stress is characterized by a stretching effect on the material’s structure, leading to elongation under stress. And, just like any other residual stress within a material or a component, tensile residual stress remains within a material in the absence of an external load.
This isn’t necessarily bad—all materials carry some degree of residual stress from manufacturing processes. However, when excessive tensile residual stress is present, it can decrease the fatigue strength of the material, leading to premature failures, such as cracking or warping.
Tensile residual stress isn’t entirely destructive—in some cases, it can be deliberately introduced to enhance the properties of a material. For example, in steel, a degree of tensile stress can improve its toughness and resistance to fracture, but an optimal balance must be maintained.
If not monitored and managed appropriately, tensile residual stress can significantly reduce an object’s reliability and overall lifespan.
Causes
Specific causes of tensile residual stresses include:
- Grinding Processes: These processes introduce heat mechanically, distorting the material and often inducing tensile residual stress.
- Shrinking/Fitting: When components cool after being heated during manufacturing, shrinkage can occur unevenly, leading to tensile residual stress.
- Bending Operations: Bending metal or steel can stretch it on one side and compress it on the other, with the elongated side undergoing tensile residual stress. Sometimes, the elongated side surface has compressive stress because of the spring effect.
- Torsional Stress: When metal is twisted, shear stress gets distributed over the cross-section, inducing tensile strain in certain areas.
- Improper Heat Treatments: If not properly managed, heat treatment processes like annealing or hardening can leave behind tensile residual stresses. Proper control of temperature and cooling rates is crucial to avoid this.
How to Measure All Types of Residual Stress
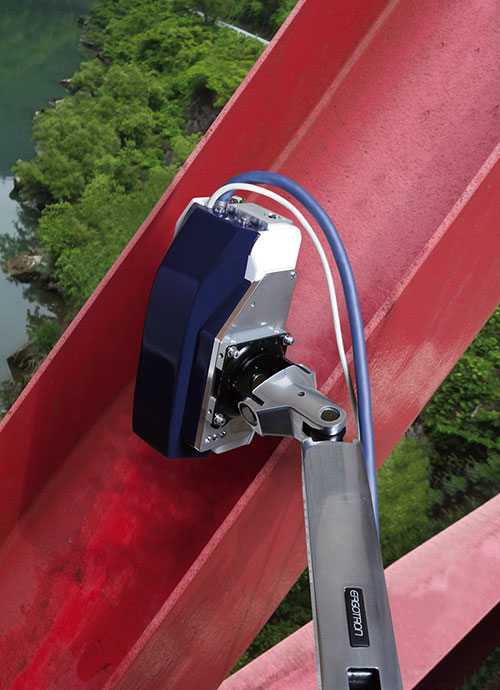
The important factor is to know polarity and the stress level on your samples either by modeling or measurement. There are numerous ways to measure residual stress, including destructive and non-destructive methods. Each technique has its advantages and caveats. If you’re eager to dive deeper into the specifics, we recommend reading more about it in our Measuring Residual Stress blog.
For a quick, non-destructive, and reliable method, consider Pulstec’s X-ray Diffraction (XRD) Residual Stress Analyzer. This tool can measure residual stress in as little as 40 seconds! It’s portable and easy to use, allowing on-site measurements without time-consuming sample preparations. Click here to learn more about our analyzer, or contact us today to request a free sample measurement or demonstration.